From garages to workshops and commercial buildings, pole barn framing offers numerous benefits for a wide range of applications. In this guide, we’ll explore everything you need to know about this building technique, including its definition, applications, pros, and cons, and more.
What Is Pole Barn Framing?
Pole barn framing (also referred to as pole building construction and post-frame construction) is a building technique that uses large posts, or poles, as the primary support for the structure. These posts are usually buried in the ground and can also be anchored to a foundation, but a foundation is not required.
Common Applications
Structures built using this building technique have the potential to replicate the functionality of many types of buildings. Some common applications include:
- Garages
- Mancaves
- Storage sheds
- Barns (farm buildings)
- Horse barns
- Horse riding arenas
- Commercial buildings
At DIY Pole Barns we offer pole building kits that can be fully customizable. Here’s an image of a commercial building from one of our customers:
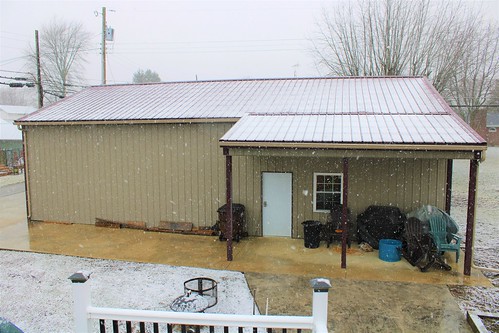
And here’s an image of a garage (from one of our customerstoo!).
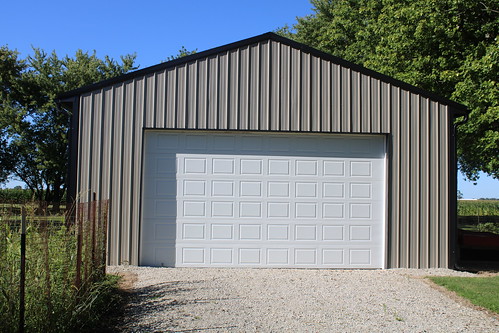
If you want to see more images like this, visit our Photo Gallery.
Advantages and Disadvantages
Pole building framing has a lot of advantages, but it also has some disadvantages to keep in mind.
Advantages
The advantages include:
Build Time
Pole barn structures are quick to build due to their simple design and lack of reliance on a foundation or basement compared to traditional building methods.
With pre-designed pole barn kits such as those offered by DIY Pole Barns, the construction process can often be completed in a matter of days, making it an excellent option for those looking to save time.
Cost-Effectiveness
Using fewer materials and requiring less labor, pole building framing is significantly more affordable than traditional construction methods.
Structural Integrity
Buried poles provide excellent stability and strength, enabling pole barn structures to withstand harsh weather conditions when built and prepared properly, including strong winds and heavy snow.
Versatility
Pole barns can be adapted for many purposes, including farm buildings, workshops, garages, and even commercial buildings. Its open interior design allows for flexible use of space, making it ideal for customized layouts and future modifications.
Take a look at our custom pole barn kitsto explore your options!
Extra Space
The absence of interior walls creates a spacious interior, perfect for storing large equipment, vehicles, or livestock. This open layout maximizes usable space.
Easy to Insulate
The simple design of pole barns makes them easy to insulate, helping to maintain energy efficiency and comfort.
Disadvantages
Some potential downsides to consider include:
Lifespan
While pole barn structures are durable, they may not last as long as buildings constructed with traditional methods. The lifespan of a pole barn can vary depending on maintenance, materials used, and environmental factors, often ranging between 40 and 60 years.
However, while 40 to 60 years is considered a safe estimation, a properly maintained pole barn built with high-quality materials can last over 100 years.
Codes and Regulations
Post-frame construction must adhere to local building codes and regulations, which can vary widely by region. Obtaining permits and ensuring compliance with local laws may require additional time and effort during the planning phase.
Rotting
The wooden poles used in this building technique are susceptible to rotting over time, particularly if they are not treated or properly protected from moisture.
Pole Barn Framing Components
Pole barn framing relies on several key components working together to create a strong and functional structure.
Here’s an image of a pole barn under construction of one of our customers for reference:
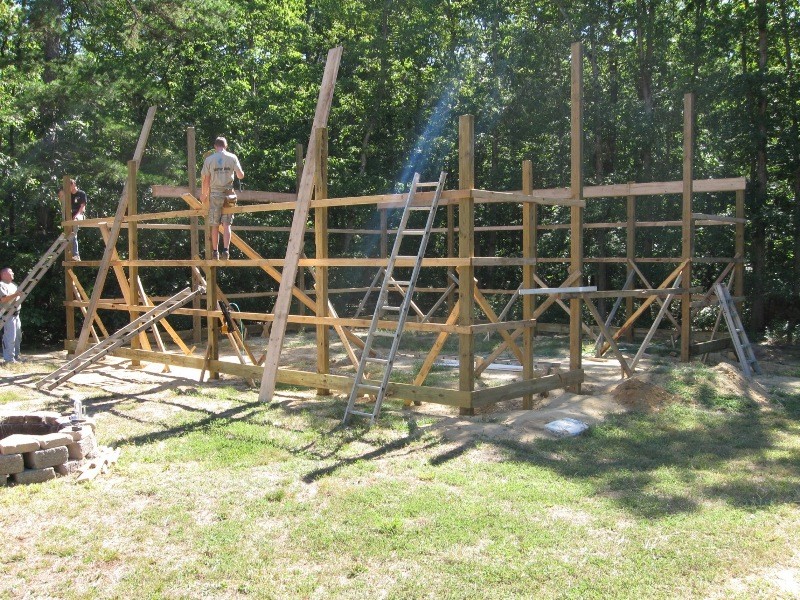
Footing/Foundation
The footing or foundation provides stability for the entire structure. Typically, poles are anchored to the ground or to an existing foundation. Local building codes usually indicate the type of foundation required for these types of buildings.
Posts
Posts are the vertical supports that bear the weight of the roof and provide stability to the whole construction.
Girts
Girts are horizontal wooden boards attached to the posts. They provide additional structural support, reinforcing the stability of the building and making it easier to attach walls to the internal side of the structure.
Trusses
Trusses are triangular frames that support the roof. They span the width of the pole barn, evenly distributing the weight of the roof and ensuring structural integrity.
Purlins
Purlins are horizontal beams placed on top of the trusses, providing additional support for the roof panels.
Skirt Board
The skirt board is a horizontal board installed along the base of the walls. It protects the building from water damage and provides additional structural integrity.
Siding
Siding forms the exterior walls of the pole barn and is typically made of metal, wood, or vinyl. It provides weather resistance and insulation.
Roofing
The roof offers protection from the elements. Metal roofing is often preferred for its durability, ease of installation, and low maintenance.
Fasteners
Fasteners such as screws, nails, and bolts hold the components together. High-quality, corrosion-resistant fasteners are essential to ensure the longevity and stability of the structure.
Factors That Affect The Cost of Your Construction
Several factors influence the overall cost of a pole barn.
Size
The size of your pole barn directly impacts the cost. Larger buildings require more materials, labor, and time to construct, which increases expenses. On the contrary, smaller structures are more affordable.
Materials
The quality of materials can increase expenses, however, this is a factor that no one should sacrifice as it directly impacts the lifespan of your building.
Labor
Labor costs depend on whether you hire professionals or complete the project yourself. DIY projects save on labor but may require more time and effort. Hiring experienced contractors ensures efficiency but increases the overall budget.
Additional Features
Adding additional features can raise the cost significantly. These enhancements improve functionality and aesthetics but require extra materials and labor during installation.
Location
The location affects everything from the cost of materials to labor rates. Some areas may incur higher transportation fees, while some locations may have costly permitting fees that add to the overall cost.
Step-by-Step Pole Building Framing Guide
Here’s a step-by-step pole building framing guide.
1. Prepare the Site
Start by clearing the site of any rocks, roots, or debris that could interfere with construction. Level the ground to create a stable base for your pole barn. Once the site is prepared, mark the exact positions where the poles will be placed, following your building plans.
2. Set the Posts
Set the poles according to your design and local building codes. You can either bury them directly into the ground (at least 3 to 5 feet deep) or anchor them onto a concrete foundation.
Whichever method you choose, ensure the poles are perfectly vertical to maintain structural integrity.
Here’s a video from our YouTube channel on how to set posts properly:
3. Install Trusses
Secure the trusses onto the poles to create the roof’s framework. This step requires precision, as trusses provide critical support for the roof.
4. Attach Siding
Attach siding to the exterior of the structure. Ensure the siding is properly aligned and secured to protect the building from the elements.
5. Install the Roof
Place roof panels onto the trusses and secure them with fasteners.
6. (Optional) Flooring and Insulation
While not essential, adding flooring and insulation can increase the functionality and comfort of your pole barn. Concrete floors provide a durable surface, while insulation helps regulate temperature and reduces energy costs if the building is heated or cooled.
History of Pole Building Framing
Pole barn framing originated in the United States during the 1930s as a response to the challenges of the depression ongoing at the time in addition to the emergence of corporate farming.
Farmers, faced with the need for cost-effective and spacious agricultural buildings, began using utility poles as the primary support structures for horse barns and other farm buildings. As the technique evolved, specific materials were developed to enhance the convenience and affordability of pole barn construction.
Over the decades, this building method gained widespread popularity, becoming a versatile solution for various applications. Today, pole barns are used for more than just agriculture. They are built for garages, storage sheds, workshops, commercial spaces, and more.
Taking the Next Step – Getting an Instant Quote
Now that you know all the details of pole barn framing, you have probably realized that building a pole barn takes a lot of time and energy in planning and construction.
At DIY Pole Barns we offer custom solutions for every need, from garages and workshops to commercial buildings. If you need a custom pole barn, we have the right solution for you!
Call our knowledgeable staff today at (937) 547-9100. You can also use our Instant Quote tool!
Frequently Asked Questions
Learn more about pole building framing.
Is Pole Barn Framing Suitable for Residential Use?
Yes, this building method is a viable option for residential use. Its open design allows for flexible layouts, and with proper insulation and interior finishes, it can be turned into a comfortable living space. It is also a cost-effective alternative to traditional home construction.
How Deep Should I Bury My Pole Framing Posts?
As a general rule, pole framing posts should be buried at least 3 to 5 feet deep to ensure stability and proper protection against the elements.
Can I Attach Other Buildings to My Pole Barn?
Yes, it is possible to attach other buildings to your pole barn. Ensure the attachment is structurally sound and complies with local building codes for safety and durability.
Pole Barn Framing: Definition, Applications & Building Guide
When folks come asking about pole barn framing, I tip my hat and tell them they’re looking into one of the most versatile and reliable ways to build, whether it’s for storing tractors, housing horses, or setting up shop. Around here, we call it post-frame construction. It’s a method that’s stood the test of time, much like a good pair of work boots.
Let’s explore what it is, how it’s used, the pros and cons, and a handy step-by-step on how to build one yourself.
What Is Pole Barn Framing?
Pole barn framing is a building method that’s known for its simplicity, strength, and cost-effectiveness. It’s commonly referred to as post-frame construction, and instead of relying on a full concrete foundation or basement, it uses large posts set deep into the ground or mounted to a footing. These posts serve as the main support structure for the roof and walls.
By shifting the structural load to these vertical posts, pole barn framing eliminates the need for load-bearing interior walls. That opens up the interior space, making it easier to use, modify, and expand. Whether you’re housing animals, equipment, or dreams, it all starts with a solid frame anchored to the earth.
Pole barn framing, also called pole building construction or post-frame construction, uses large vertical posts, usually buried in the ground or anchored to a concrete footer, as the structural backbone of the building. These posts support the roof and walls, which means fewer interior walls and a more open interior layout.
Common Applications of Post-Frame Buildings
You’ll find pole barns just about anywhere. Here’s where they shine:
- Garages and workshops
- Mancaves and hobby buildings
- Storage sheds
- Barns and livestock shelters
- Riding arenas
- Commercial buildings
Our team at DIY Pole Barns has helped build all kinds of these—from backyard garages to full-on business spaces. Want to see some examples? Visit our Photo Gallery to browse real customer builds and get inspired for your own project.—from backyard garages to full-on business spaces. Browse the Photo Gallery on our website to see examples from folks just like you.
Pros and Cons of Pole Barn Framing
Advantages
Quick Build Time
These buildings go up fast. With no basement or heavy foundation work, you can be raising walls in days.
Cost-Effectiveness
Fewer materials and less labor means you get more for your money.
Strong and Durable
Properly installed posts and trusses can withstand high winds and snow loads. With good maintenance, they’ll hold up for generations.
Flexible Layouts
Need a big open space? No problem. Want to add walls or rooms later? You can.
Room to Spare
No load-bearing interior walls means more usable floor space—great for large equipment, livestock, or big gatherings.
Easy to Insulate
The clean framing design makes it simple to add insulation and keep things comfortable year-round.
Disadvantages
Lifespan
Expect 40 to 60 years on average. With quality materials and proper upkeep, you might see well over 100.
Permits and Codes
You’ll need to check with your local authorities. Requirements vary from county to county.
Moisture Issues
Untreated wood in the ground can rot. We use treated posts and smart design to keep moisture at bay.
Core Components of a Pole Barn
Here’s what you’ll typically find in one of our kits:
Footing/Foundation
Supports the structure. The foundation is where it all begins. Depending on the design, posts can either be set directly into the earth—usually 4 feet deep—or attached to concrete piers or slabs using engineered brackets. This approach allows flexibility for different soil conditions and load requirements, while keeping material costs manageable.. Posts can be set 4 feet deep into the ground or anchored to a concrete slab.
Posts
These bear the building’s weight. Posts are typically spaced 8 feet apart, though spacing may vary by design. At DIY Pole Barns, our standard is to set each post 4 feet into the ground unless otherwise specified by site conditions or engineering. Treated for ground contact, these posts are built to endure years of exposure and pressure while serving as the vertical backbone of the structure.. Our standard depth is 4 feet, but plans vary depending on soil and climate conditions.
Girts
Horizontal supports attached to posts that help reinforce the frame and support siding.
Trusses
Triangular roof frames that span the width and carry the load. Trusses are engineered to your building’s specific span, pitch, and load conditions. Whether you’re dealing with snow loads in Michigan or wind gusts in Oklahoma, our trusses are designed to hold strong and hold steady.
Purlins
Horizontal boards on top of the trusses that support roofing panels.
Skirt Board (Grade Board)
Sits at the base of the wall to provide stability and water protection.
Siding
Metal is most common, but you can also use wood or vinyl.
Roofing
Typically metal for longevity, low maintenance, and easy installation.
Fasteners
Corrosion-resistant screws, bolts, and nails that hold everything together.
What Influences the Cost of a Pole Barn?
- Size – More square footage means more materials and more labor.
- Materials – Higher quality means higher cost up front, but longer lifespan.
- Labor – DIY saves money but takes time. Hiring pros costs more but saves your back.
- Extras – Doors, windows, overhangs, and insulation all add to the final total.
- Location – Delivery fees, local material pricing, and permit costs vary by region.
Step-by-Step Pole Barn Building Guide
Need help visualizing the process? Check out our How to Set Posts Video on YouTube. It walks you through one of the most important steps in getting your pole barn off to a solid start.
1. Prepare the Site
Clear out rocks, roots, and debris. Level the area and mark post locations based on your plans.
2. Set the Posts
Standard depth is 4 feet. Posts must be plumb and square. You can also use brackets on a concrete foundation if your plan calls for it.
3. Install Trusses
Attach to the posts to form the roof frame. Brace everything temporarily until it’s all locked in.
4. Attach Siding
Metal panels are secured to the girts. Align them carefully and fasten them tight.
5. Install Roofing
Lay roofing panels over the purlins and fasten according to the manufacturer’s specs.
6. (Optional) Add Flooring and Insulation
Concrete floors make cleanup easy. Insulation helps if you plan to heat or cool the building.
A Look Back: The History of Pole Barn Framing
The roots of pole barn construction stretch back to the agricultural ingenuity of the 1930s. Facing the Great Depression and a shift toward larger-scale farming, rural builders started reusing telephone poles and other round timbers to create spacious, affordable barns. This no-nonsense approach evolved over the decades into modern post-frame engineering, incorporating advanced materials and better fasteners. What hasn’t changed is the heart behind it: solving problems with integrity, resourcefulness, and a can-do attitude.
Pole barns began in the 1930s, when farmers needed big, strong buildings on tight budgets. They used old telephone poles for framing. That resourcefulness grew into what we now call post-frame construction. Today, we’ve got better tools and materials, but the goal’s the same: build smart, build strong, and make it last.
Taking the Next Step
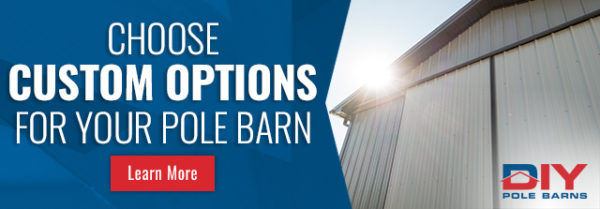
Now that you know what goes into pole barn framing, it’s time to take action. At DIY Pole Barns, we’ve got custom kits, pre-engineered plans, and a team ready to walk you through it all.
Call us at 800-622-4242 or use our Instant Quote Tool to get pricing tailored to your needs. Whether you’re dreaming big or starting small, we’re here to help you build it right. Let’s build something strong, smart, and built to last.
Until next time,
-Albert Barnwright
Tool Belt Tightener, Post Hole Ponderer